Home » Articles posted by Lucas Tyler
Author Archives: Lucas Tyler
Shaping the Future of Building through Modern Contractor Practices
Contractors Murfreesboro TN today are no longer confined to simply executing construction blueprints. They have evolved into multi-skilled professionals who manage every aspect of a project from concept to completion. This transformation is driven by the demand for precision, sustainability, and cost efficiency. As a result, the role of contractors has become more dynamic and complex than ever.
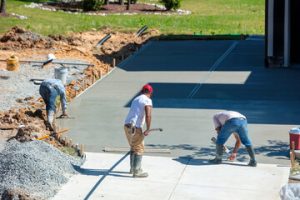
One of the emerging roles of modern contractors is their involvement in early-stage planning. Instead of waiting for final designs, they now collaborate with architects and engineers to influence material selection, layout, and workflow. This allows them to identify cost-saving opportunities and reduce waste before construction begins. The result is a more streamlined project that benefits both clients and the environment.
Technology integration has significantly reshaped how contractors operate. Digital modeling tools and project management software allow them to track progress in real time. This improves communication among all stakeholders and minimizes costly delays. The ability to visualize outcomes before work begins also helps reduce design errors.
Sustainability is becoming a central focus in the contractor’s work process. Many are adopting eco-friendly building methods, such as using renewable materials and incorporating energy-efficient systems. This shift not only meets regulatory requirements but also aligns with the growing consumer preference for green living. It ensures that projects remain relevant in a rapidly changing market.
Safety management remains a top priority for contractors in every sector. The use of wearable sensors, automated monitoring, and predictive analytics helps identify risks before they lead to accidents. By integrating safety into every stage of the project, contractors can protect their teams and maintain productivity. This proactive approach is now considered essential in the industry.
Specialization among contractors is also becoming more common. Some focus on niche markets such as modular construction, heritage restoration, or high-performance insulation systems. This allows them to deliver highly tailored services and build expertise in specific techniques. Clients often prefer specialized contractors for their depth of knowledge and precision work.
Modern contractors are increasingly involved in the circular economy. Instead of discarding excess materials, they find ways to recycle, reuse, or repurpose them in other projects. This practice reduces costs, lowers environmental impact, and creates new revenue streams. It also enhances their reputation as forward-thinking professionals.
Logistics management has taken on greater importance in large-scale projects. Contractors now coordinate complex supply chains, ensuring that materials arrive on time and in the right sequence. Delays in delivery can have a domino effect on the entire project schedule. Effective logistics planning keeps projects running smoothly and within budget.
In remote or challenging locations, contractors must adapt their strategies to local conditions. This can include modifying building methods to suit climate, terrain, or available resources. Flexibility in problem-solving is a valuable skill that can determine the success of a project. These adaptations also lead to innovative techniques that can be applied elsewhere.
Client communication has evolved from occasional updates to continuous engagement. Contractors now use digital dashboards and instant messaging platforms to keep clients informed daily. This transparency builds trust and allows for quick decision-making when changes are needed. It also reduces misunderstandings and disputes.
The contractor’s role in workforce development is becoming more prominent. Many are investing in training programs to upskill their teams in advanced construction techniques and digital tools. This ensures that workers remain competitive in a fast-changing industry. It also contributes to higher quality outcomes and greater efficiency.
In the realm of cost control, contractors are adopting advanced forecasting methods. Data analysis allows them to predict expenses more accurately and adjust plans before overruns occur. This helps maintain financial stability throughout the project. Accurate budgeting also enhances client satisfaction and trust.
Environmental resilience is another area where contractors are making strides. They are incorporating designs and materials that can withstand extreme weather events. This ensures the longevity of structures and reduces repair costs over time. It also meets the growing need for climate-adaptive construction.
Contractors are now key players in integrating smart technologies into buildings. From automated lighting systems to energy monitoring solutions, they ensure that new structures are future-ready. These installations improve functionality and lower operational costs for occupants. This added value is becoming a major selling point in the market.
Collaborative contracting models are gaining traction in the industry. Instead of adversarial relationships, contractors, designers, and clients work together toward shared goals. This reduces conflicts and accelerates project delivery. It also fosters innovation by encouraging the exchange of ideas.
In industrial projects, contractors often take on the role of compliance managers. They ensure that construction processes meet strict safety, environmental, and operational regulations. This prevents costly penalties and keeps projects legally secure. Their expertise in navigating these requirements adds a layer of assurance for clients.
Disaster recovery projects have also become a specialized field for contractors. In the aftermath of natural or man-made disasters, they must work quickly to assess damage and rebuild essential infrastructure. This requires rapid mobilization, resource management, and community coordination. Their ability to restore functionality is critical for affected areas.
Cultural sensitivity is an important factor for contractors working in diverse regions. Understanding local traditions, materials, and design preferences can lead to better community acceptance of a project. This approach fosters goodwill and reduces opposition during construction. It also enriches the final design with locally relevant features.
The competitive landscape is pushing contractors to differentiate themselves through innovation. This could mean adopting robotics for repetitive tasks, using drones for site inspections, or implementing AI-driven quality checks. Such advancements improve accuracy, speed, and overall project quality. Staying ahead in technology adoption can define long-term success.
Future trends suggest that contractors will become even more integral to shaping sustainable cities and communities. Their expertise will extend beyond construction into urban planning, renewable integration, and adaptive reuse of spaces. This evolution positions them as central figures in the transformation of the built environment. As demands grow, their ability to adapt will determine the industry’s direction for decades to come.
The Ultimate Guide to Interior and Exterior House Painting
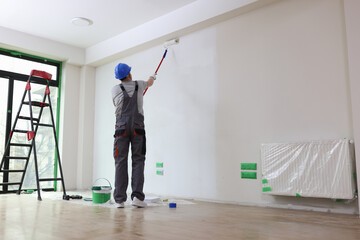
Painting is one of the most transformative and cost-effective ways to refresh your home. It can dramatically improve the ambiance, showcase your personal style, and protect the underlying surfaces from moisture, dust, and daily wear. However, achieving flawless results requires thorough preparation and expert techniques. This guide will walk you through everything you need to know about interior and exterior house painting.
Preparation
A fresh coat of paint can do wonders for your home’s appearance and value. It can transform a dull exterior into something eye-catching and beautiful, or it can protect your investment from weather damage. However, a quality paint job requires careful planning and preparation. Choosing the right paint, hiring professional Modesto House Painters, and properly preparing surfaces are all important steps in ensuring that your new interior or exterior paint will last for years to come.
In addition to being a great way to improve your home’s aesthetic, a new paint job can also help make it feel more welcoming and personal. The right colors can elevate your space from feeling sterile and cold to a place where you truly love to be. If you’re in the market for a new paint color, it’s important to research what types of paint are available and understand how they differ from one another. This will ensure that your new paint will be able to meet your specific needs, and it can help you avoid any costly mistakes down the road.
Once you’ve decided on the perfect paint color, it’s time to start preparing your walls for the project. This step can include everything from washing the surface with a power washer (only on durable surfaces) to wiping them down with a damp cloth and cleaning up any residue. It’s also important to remove any loose pieces of wood or molding and fix them before you begin painting. Quality painting contractors will know that a good prep job can make or break the result of your final paint job.
It’s also a good idea to move any furniture out of the room, or cover it with plastic sheets to prevent scuff marks and spills. This will give the painting contractors a clean and open workspace to work in, and it will also prevent any accidental scuffing of your valuable furniture. Lastly, you should cover any plants and shrubs that are in the vicinity of your house to prevent them from getting dirty or wet.
By taking the time to properly prepare your house for painting, you’ll be able to achieve a flawless and long-lasting finish. This will save you money in the long run by reducing the need for frequent touch-ups and repainting, and it will also ensure that your new paint will stand up to Northern Virginia’s challenging weather conditions.
Color Selection
Color selection is a critical step in any painting project, and it can greatly affect the overall results of your home’s interior or exterior. It’s important to consider a variety of factors when selecting paint colors, including your desired emotional response, the purpose of each room, and local climate conditions. Consultation with a professional can help you navigate these challenges and ensure the best possible outcome for your home.
For example, warm hues such as reds, oranges, and yellows can create a feeling of warmth and welcome, making your home seem more welcoming to guests and passersby. In contrast, cool tones such as blues, greens, and purples tend to exude serenity and sophistication. It’s also important to consider the architectural style of your home and any existing elements that will be painted, such as windows, doors, roof, and hardscape. A professional can help you select a color scheme that complements your home’s unique features while remaining consistent with your vision.
As you consider your options, it’s a good idea to purchase small samples of each color and test them on your home’s exterior in various lighting conditions. For example, you may find that a shade looks vibrant and inviting in the soft light of early morning but fades quickly under the bright sunlight of midday.
Finally, be sure to take into account the maintenance requirements of your chosen shade. Some colors are more vulnerable to wear and tear than others, so it’s important to select a durable coating that can withstand harsh weather conditions without fading or chipping.
Choosing the right color for your home can be an overwhelming task, but it’s important to strike a balance between current trends and your personal preferences. Remember, it’s a long-term investment in your property, so you should select a palette that will make you proud for years to come. Test your choices in various lighting conditions and consult with a professional to avoid costly mistakes.
Painting Techniques
A fresh coat of paint can completely transform a house and increase its value. However, achieving a flawless finish requires proper preparation, the right materials, and skilled application techniques.
Whether you want to create a cozy ambiance in your living room or a relaxing environment in your bedroom, interior painting provides endless possibilities. But it’s not just about applying color to walls—it’s about creating the right mood and boosting your home’s curb appeal.
To achieve the perfect look, you need to consider your home’s lighting conditions, surroundings, and architectural style. Then, you can select the ideal color combination. For example, a light blue for the body and crisp white for trim and accents can give your home a coastal feel.
Moreover, you need to choose the correct paint for the surface you’re painting. Different surfaces require different paints to ensure adhesion and durability. You also need to consider the climate, humidity, and temperature fluctuations that can affect your paint job. Finally, you should use a high-quality primer to ensure that your paint lasts longer and protects your surface from moisture and sunlight.
Hiring professional interior painters is the best way to ensure quality results. They can provide advice on selecting the right colors and finishes and recommend the best painting techniques for your space. They also have the necessary tools for the job, such as a variety of brushes and rollers that cater to different surfaces and textures.
Besides providing a smooth and even coat, professional painters will also make sure that the paint dries properly. They will inspect the surface under both natural and artificial light to identify any missed spots or uneven areas. They will also clean up and remove any wall decorations, such as pictures or mirrors. And they’ll take down curtains, blinds, and other window treatments to prevent them from getting dirty or splattered with paint. In addition, they will use plastic sheeting and drop cloths to protect them from dust and paint splatters. Lastly, they will carefully cover furniture and other objects that you don’t want to get painted.
Why You Should Hire a Professional Mover
Ox Movers Spring TX have a lot of tools for getting the job done. From professional-grade packing materials to dollies, loading ramps and roomy moving trucks. They have everything they need to get your stuff from Point A to Point B safely and quickly.

When hiring movers, check their customer service and availability. Also, ask for references and read their contracts carefully.
A good moving company has a team that is experienced in handling various types of items. They know how to handle furniture, boxes, and other large items properly to ensure that they are not damaged during the process. This is particularly important for long-distance moves, which require a lot of planning and coordination to make sure that your belongings reach their destination safely.
Besides experience, you should also consider the reputation of the company. You can do this by checking online reviews and feedback from past customers. This will help you decide whether to hire the company or not. Look for companies with a solid track record of being punctual and providing quality service to their clients.
It is also important to note that a good moving company should be insured and licensed. This will protect you from any liabilities that may arise during the move. This will also ensure that your belongings are in safe hands, and that you can get them back if anything goes wrong. Additionally, a good moving company should be able to provide you with a written quote of all the services they will provide you with, including any extra fees.
When hiring movers, it is important to remember that they are handling your most valuable possessions. You should make sure that they are reliable and trustworthy, and you should never leave them unattended during the move. You should also read through their customer reviews to see if they are honest and have a good reputation.
You should also check if the movers are punctual and provide accurate time estimates. If they show up late or miss their deadlines, it is a sign that they are not reliable and should be avoided. Moreover, you should also look at their social media accounts to see if they are active and have a good following.
When choosing a moving company, it is important to survey multiple candidates and choose the one that best fits your needs and budget. It is also a good idea to read reviews from other customers and look for a company that has transparent pricing. This way, you will not be surprised by any hidden fees or unexpected charges.
Efficient
A good moving company has a pool of vehicles, the latest equipment, and trained workers who know how to handle and pack things. They also know how to use these vehicles in the best possible way, avoiding any damage or loss of items during transit.
In addition, you can improve the efficiency of your service by offering add-on services, such as storage, packing, or furniture assembly. This will allow you to upsell more services to your customers and increase your revenue. However, the decision to outsource or take on these additional tasks may come down to personal preferences and comfort levels.
Saves You Time
Professional movers have the expertise to handle all the heavy lifting for you, saving you time and energy. You’ll have more time to devote to other aspects of your move, like arranging travel plans for your family or finding work in your new city.
Moving is a complex process. Getting rid of items you no longer use, cleaning and organizing the space, packing boxes, transporting everything on a truck or in a container, and unpacking all your belongings is a lot to take on by yourself. Whether you’re a busy family with lots of kids, a senior citizen with limited mobility or an injured service member, hiring professional movers can make the transition to your new home much smoother and easier than it would be by yourself.
When you hire a professional moving company, they’ll come prepared with all the tools and equipment needed to handle your move. This saves you time and effort from having to find, purchase or borrow a moving truck, renting moving supplies, cleaning and packing materials, and decluttering your home.
Hiring a full-service moving company also eliminates the need to rent or purchase a rental truck, which saves you money on gas, wear and tear on your vehicle, and any damage that could result from driving over a load of heavy furniture. You’ll also have peace of mind knowing that your belongings are in good hands with a reliable moving company who provides insurance coverage for their services.
To save time on moving day, prepare for movers in advance by starting to pack non-essential items one to two weeks before the move. This will give you a chance to double check your inventory sheet and high value items to make sure you’ve packed all that needs to be moved. It’s also helpful to measure large items (refrigerators, couches) and narrow doorways before you bring in movers, as this will help prevent the need for disassembly. And finally, if you have children, it’s a great idea to arrange for them to play at the homes of friends or relatives on moving day so you can focus on them and avoid distractions.
Saves Money
Whether you’re moving your business or your family, moving can be expensive. But there are ways to save money when you move. By following a few simple tips, you can minimize the cost of your move without sacrificing quality or service.
One way to save money on your move is to shop around for the best price. Compare prices between different moving companies and make sure you get an accurate quote before booking a service. You can also reduce your costs by properly packing and organizing your belongings. It is important to use durable boxes and tightly pack items so they are protected from damage. Another tip is to avoid using multiple boxes, as this can increase the weight of your shipment and lead to costly damages.
If you decide to save money by doing your move yourself, it’s important to consider the costs of renting a truck, gas, insurance and mileage. These expenses can add up quickly, making the DIY option a more costly choice in the long run. Additionally, DIY moves require a lot of time and physical labor. It’s easy to strain muscles and aggravate back problems during the process. Professional movers are experienced in handling heavy loads, preventing injuries and saving you the expense of doctor visits or hospital bills.
Professional movers charge by the hour and their services are often based on the weight of your shipment and the distance they travel. To save money, you can minimize your shipment weight by sorting through your belongings and donating or selling items you no longer need.
When packing, it’s also a good idea to organize your boxes by size. This will save you time and money by allowing movers to stack your boxes more efficiently in the truck. In addition, by keeping your boxes organized, you’ll make it easier for yourself to find the things you need when unpacking. Finally, don’t forget to purchase high-quality packaging materials and use a strong tape to secure your boxes. This will ensure your belongings are safe and protected during the move.
Advantages and Disadvantages of Plastic Molds
American Plastic Molds are a vital component of the plastic injection molding process. They’re expensive to produce, require a lengthy wait time, and are often made of steel or aluminum.
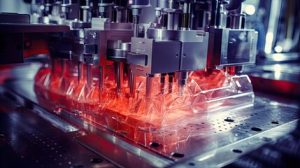
Proper mold structure design helps to lengthen their lifespan. Slower cycle times also enhance durability. However, there are several factors that can cause damage to plastic injection molds.
Liquid injection molding (LIM) is a specialized process for creating high-consistency elastomers and silicone rubbers. The unique liquid form of this material provides many advantages over traditional molded parts and opens up new possibilities for product designs. LIM is used for products in a variety of industries, including automotive, medical, electronics, and textiles. It is particularly useful for products that require a precise shape, tight tolerances, and stringent flash requirements.
The primary components of the LIM process are two liquid materials, a base-forming silicone and a catalyst. They are dispensed through a pumping system that includes a metering unit and a static mixer. The metering unit and mixer combine the materials into a mixture that is injected into the mold. A nozzle directs the flow of the mixture into the mold, where it hardens into the desired shape of the final product.
Due to its low viscosity, the liquid-like silicone requires a very stable mix to keep it from becoming clogged in the metering unit and mixer. To minimize these problems, a spring-loaded pin nozzle is often used in the metering unit to help prevent clogs and blockages. The nozzle also helps to maintain proper gating, which reduces the possibility of air traps and weld lines.
The nozzle is also designed to deliver the mixture at the proper rate for the injection and cure processes. This ensures that the mixture is evenly distributed throughout the cavity and prevents premature foaming. In addition, the nozzle has an automatic shut-off valve to avoid overfilling. This feature is especially important for elastomeric parts, where overfilling can cause a poor finish.
After the nozzle dispenses the mixture, the resulting cured silicone is injected into the mold to create the finished part. The process is quick and efficient, and the resulting product has excellent tensile strength. It is also resistant to abrasion and moisture.
The injection and curing processes are controlled by an automated injection machine with a set of custom programming. These settings are based on the customer’s part design and can include temperature, pressure, injection rates, and cycle time. The automated machine also has a platen system to align and close the molds, and a piston to apply the necessary injection pressure.
Extrusion moulding
Extrusion moulding is a great option for creating long-length plastic products. This method allows you to continuously produce long tubular components with a high degree of accuracy, which can reduce production costs and machine downtime. It also minimizes waste and allows for excess plastic to be gathered and used in future projects. This process is especially useful when producing a product with a large cross-section, such as industrial piping or synthetic filaments.
The extrusion moulding process starts with plastic granules that are stored in a hopper before they’re heated inside a barrel known as an extruder. The granules are then forced through a shaped die, which gives them the desired shape. The resulting linear workpiece is then cooled before it can be cut into plastic parts. The process can be used to create a wide variety of linear products, including food packaging, synthetic filaments, and even drinking straws (coextrusion).
Advantages of Extrusion Moulding
The primary benefits of plastic extrusion moulding include its cost-efficiency, flexibility, and versatility. It’s a good choice for long, elongated products that need to be made with a consistent cross-section, such as pipes, rods, and wires. In addition, extrusion can be used with a wide range of materials, from thermoplastics to metals. It can also be used for products that require a smooth surface and specific textures.
In contrast, injection molding has several disadvantages, ranging from high initial tooling costs to environmental concerns. Its high energy consumption during heating and cooling, along with its limited durability, raise questions about its sustainability. It also does not scale as well as extrusion, which limits its production potential.
Both processes have their benefits and drawbacks, but extrusion is better for making longer plastic items, such as tubes or rods. Injection molding, on the other hand, is better suited for shorter components that need to be precise in size and alignment. However, extrusion has its own unique advantages, such as its ability to produce long lengths of a single plastic material. It’s also great for producing a wide range of colors and textures, which makes it an ideal choice for plastic projects that need to look appealing.
Continuous moulding
Continuous moulding is a versatile process that offers advantages such as shorter cycle times and lower production costs. It is suitable for producing a variety of products, from small, symmetrical items to complex and long-range products. This method is particularly useful for making replacement parts for broken metal items, as it produces very strong and durable results. It also allows for the use of recycled materials.
In this method, a powdered resin is loaded into a hollow mold that is securely closed and heated to melt the polymer. The molten plastic is then fed into a die that gives the final shape to the product. The polymer is then cooled and trimmed to complete the cycle. The advantages of continuous molding are numerous, including the ability to produce complex shapes with high accuracy and precision. It is also an economical and fast way to make replacement parts for damaged metal products.
The main advantage of continuous moulding is its ability to reduce waste, which can be a significant cost in other manufacturing processes. It also produces a uniformly-sized finished product, which is critical for mass production. Additionally, continuous moulding produces a finished part with an extremely smooth surface. This makes it easy to apply coatings, printing, and graphics to the surface of the finished product.
To ensure the quality of a continuous-cast product, the temperature of the molten metal and the speed of cooling need to be closely monitored. In addition, the molten metal must be evenly distributed between the walls of the mold. This can be achieved by using a combination of a cooling system and roller support. A primary additive to the molten metal can improve its flow characteristics during the casting process, while a heat stabilizer prevents thermal degradation.
The most common material used for continuous cast is a blend of low-density and high-density polyethylene. This polymer has excellent chemical and fatigue resistance. It is also readily available in a powdered form and has good flow properties, which makes it suitable for rotational molding. In addition, a range of secondary additives can enhance the mechanical properties of the finished product.
Pressure moulding
Pressure moulding is a process used to produce products that require high levels of detail and precise shapes. This manufacturing method offers many benefits, including low tooling costs and rapid production cycles. However, it is not without its limitations. In order to make the most of this process, it is important to understand its strengths and weaknesses. This will help you determine whether it is the right choice for your project.
The pressure forming process uses heated plastic sheets to shape them over a mold. This is an ideal process for producing thin-walled designs, such as medical devices and automotive components. It is also able to handle a wider range of shapes than vacuum forming. This flexibility is particularly beneficial for companies that need to bring products to market quickly.
However, the high-pressure used in this process can cause thickness variations in the finished product. Inconsistent thickness can lead to weaker areas in the final product, compromising its structural integrity and performance. These variations are caused by the way that the heated plastic material flows during forming. A combination of factors can reduce these variations, including strategic vent placement and optimized mold contours. In addition, using thermoplastics with good elongation and flow characteristics can improve consistency.
Another benefit of pressure forming is that it produces a more uniform part than vacuum forming, due to the fact that the material is heated under constant pressure. Injection molding is a more effective option for manufacturing parts that need to be extremely smooth, though, as it is better equipped to handle complex geometries and thicker materials.
Injection molding is also a better choice for producing larger parts, as it has a greater injection volume than other processes. However, it is important to keep in mind that the pressure of the injection molding machine should be matched to the projected area of the plastic part. Otherwise, uneven heating can occur and the resulting part may be warped or damaged. Likewise, the injection temperature should be adjusted accordingly. Lastly, the injection mold should be designed to allow for quick cooling after injection.
Stucco Removal – What You Need to Know
There comes a point in most homeowners’ lives when they will have to consider stucco removal. This may be due to an underlying issue such as moisture intrusion or shoddy initial installation that has led to extensive damage over time.
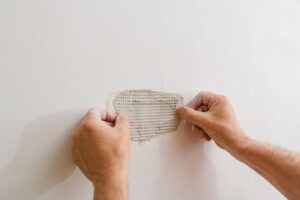
Begin by scoring the stucco in a hidden area. Draw guidelines using chalk to determine how large of a chunk you are comfortable removing at a time. Contact Stucco Removal now!
Stucco is a common exterior wall covering that has been around for thousands of years. It is a variety of plaster that consists of sand, cement and water, and it can be applied in many different ways to create a unique look. It can be textured, colored and tinted to suit your home, and it will last for many years without needing extensive maintenance.
It is also fire-resistant, which makes it a great choice for homes in hotter climates. If you’re thinking about adding stucco to your home, it’s important to know the benefits and downsides of this type of siding.
The first step in removing stucco is to prepare the worksite. This usually involves laying tarps to contain any debris and assembling scaffolding, if necessary. The workers will then use a circular saw to cut through the top layer of stucco. The next step is to use a hammer or crowbar to remove any loosened pieces. The workers will continue this process until all of the stucco has been removed.
Once the workers have finished removing the stucco, they will clean the wall surface. This is important because stucco can be ruined by high accumulations of moisture. Moisture can cause mold, which can then wreak havoc on the structure of your home. This is especially true if you live in an area with a high humidity level.
You should also clear the area that you plan to stucco. It’s best to remove all paintings and rugs from the area, as well as cover any furniture that isn’t too heavy to move. This will help the adhesive cement to stick better to the wall surface and prevent it from leaking or staining anything underneath it.
Once you have the wall clean, you can begin applying the first base coat. This coat is known as the scratch coat, and it’s typically made from a mix that’s slightly different from the finish coat.
Apply this coat until it’s about a quarter inch thick. If you’re working outdoors, you should spray it with a light mist of water to keep the mixture workable. Then, allow the brown coat to dry for about 10 days.
Reputable Businesses
Stucco is a popular building material that’s used on a variety of structures including single-family homes. It’s an attractive option that provides a wide range of benefits, such as energy efficiency and moisture control. It also adds a distinctive look to your home, but like any product it needs proper care to maintain its condition and function.
When your stucco becomes damaged, it’s essential to call a professional immediately to prevent further damage and protect the value of your investment. If moisture seeps through the stucco, it can destroy the walls and even threaten the structural integrity of your home. It’s a good idea to keep an eye out for warning signs that you should get your stucco repaired, such as exterior cracks, damage, and stains.
A reputable stucco remediation company will conduct a thorough inspection of your siding to determine if there are any underlying issues that need to be addressed. They’ll take into account things such as sagging sheathing, exposed framing members, and the presence of mold or water damage. They’ll then recommend the best course of action to correct the problems.
Once the problem is identified, they’ll remove any existing stucco and install a new layer. They’ll also reinstall sheathing and re-attach the metal lath that supports the stucco. In addition, they’ll inspect your landscaping and interior openings such as windows to ensure that they are protected from harm during the process.
Depending on the extent of the damage, your remediation may include removing and replacing drywall as well. They’ll then clean and prime the walls before they apply the new stucco coat. During this process, they’ll ensure that the new coating adheres properly to the wall and that no gaps are left between it and the sheathing.
It can be difficult to determine whether your stucco requires repair or remediation, especially if you’re not familiar with the difference between the two services. Remediation is a more comprehensive service than simple repair, so it’s important to find a business that can provide both services when necessary.
Safety
As a homeowner, it’s important to consider safety measures when undertaking a stucco removal project. This is because sand and concrete are incredibly hard and dense, which can lead to injuries and property damage if not handled properly. For this reason, it is recommended that you have a friend assist you with the job or hire a professional to handle the work for you. It is also advisable to wear protective clothing such as gloves and goggles during the process.
A few decades ago, stucco enjoyed a period of popularity as an exterior aesthetic choice, and many people opted to cover their brick and mortar walls with this material. However, the truth is that stucco is a poor insulator and can cause moisture problems in homes and buildings. This is because it has a high water absorption rate, which can lead to rot, mold and other structural damage.
This moisture can be caused by a number of different things, including heavy rains and high humidity levels. It can also occur as a result of insufficient ventilation, which leads to the buildup of condensation. This, in turn, can cause a white, powdery substance known as efflorescence or, more severely, a crumbling surface that’s called cryptoflorescence.
To avoid this, it is essential to have your stucco repainted and resealed every few years. These coatings act as a barrier, stopping some of the moisture from penetrating the surface of the wall. However, they can also degrade over time. This leaves your walls vulnerable to moisture damage, which can worsen over time and result in costly repairs.
It’s also a good idea to regularly inspect your stucco for signs of damage. Doing so can help you identify problems early on, and you can take steps to correct the problem before it gets worse. This is especially important if you live in an area with a lot of rain or other weather conditions that can cause water damage to stucco.
Taking the time to inspect your stucco can save you a lot of money and prevent expensive repairs in the future. If you are unsure about how to properly care for your stucco or don’t have the necessary endurance and strength to do it yourself, contact a reputable stucco company like Patch Dudes for assistance. They’ll be able to provide you with a free quote and can handle the entire job for you.
Time
As with any project, there are factors beyond the control of both you and your contractor that can affect how long it takes to complete stucco removal. These may include weather conditions, material shortages and labor availability. These issues should be discussed with your contractor prior to starting the project and will help to determine how much time you should budget for the job.
Depending on the type of home you have, the type of foundation and the amount of stucco to be removed, it can take anywhere from a day to several weeks for the crew to finish their work. In addition, there is often a significant amount of debris left behind that will need to be cleaned up and hauled away. This can add to the overall cost of your project.
Stucco is an insulating siding that adds value to your home, but it can also be prone to damage. These problems can range from hairline cracks to severe structural damage that requires a costly repair. Regardless of the cause, it is important to address these issues as quickly as possible to avoid allowing them to worsen and possibly compromise the integrity of your house.
Cracks in stucco are common due to a number of factors including poor installation, changes in temperature and even the settling of your house. Cracks that are not addressed quickly can result in a loss of energy efficiency and moisture penetration that will lead to mold and mildew.
Inspecting your stucco on a regular basis can help you to catch small or larger damage before it becomes a major problem. A good rule of thumb is to walk the perimeter of your home on a regular basis, usually monthly, and assess any areas where there are signs of damage such as chips, cracks or other discoloration.
Keeping your stucco clean can be done on a regular basis by spraying it with water using a hose or pressure washer. This will remove dirt and biological growth that can make your home look unsightly and it can also help prevent surface damage. To get rid of green algae that is growing in the pores of your stucco, you can use a solution made from non-chlorine bleach and white vinegar. This mixture will draw the fungus to the surface, where it can be scrubbed with a brush and then rinsed with water.