Home » Plastic Manufacturing
Category Archives: Plastic Manufacturing
Advantages and Disadvantages of Plastic Molds
American Plastic Molds are a vital component of the plastic injection molding process. They’re expensive to produce, require a lengthy wait time, and are often made of steel or aluminum.
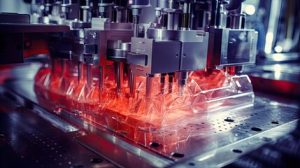
Proper mold structure design helps to lengthen their lifespan. Slower cycle times also enhance durability. However, there are several factors that can cause damage to plastic injection molds.
Liquid injection molding (LIM) is a specialized process for creating high-consistency elastomers and silicone rubbers. The unique liquid form of this material provides many advantages over traditional molded parts and opens up new possibilities for product designs. LIM is used for products in a variety of industries, including automotive, medical, electronics, and textiles. It is particularly useful for products that require a precise shape, tight tolerances, and stringent flash requirements.
The primary components of the LIM process are two liquid materials, a base-forming silicone and a catalyst. They are dispensed through a pumping system that includes a metering unit and a static mixer. The metering unit and mixer combine the materials into a mixture that is injected into the mold. A nozzle directs the flow of the mixture into the mold, where it hardens into the desired shape of the final product.
Due to its low viscosity, the liquid-like silicone requires a very stable mix to keep it from becoming clogged in the metering unit and mixer. To minimize these problems, a spring-loaded pin nozzle is often used in the metering unit to help prevent clogs and blockages. The nozzle also helps to maintain proper gating, which reduces the possibility of air traps and weld lines.
The nozzle is also designed to deliver the mixture at the proper rate for the injection and cure processes. This ensures that the mixture is evenly distributed throughout the cavity and prevents premature foaming. In addition, the nozzle has an automatic shut-off valve to avoid overfilling. This feature is especially important for elastomeric parts, where overfilling can cause a poor finish.
After the nozzle dispenses the mixture, the resulting cured silicone is injected into the mold to create the finished part. The process is quick and efficient, and the resulting product has excellent tensile strength. It is also resistant to abrasion and moisture.
The injection and curing processes are controlled by an automated injection machine with a set of custom programming. These settings are based on the customer’s part design and can include temperature, pressure, injection rates, and cycle time. The automated machine also has a platen system to align and close the molds, and a piston to apply the necessary injection pressure.
Extrusion moulding
Extrusion moulding is a great option for creating long-length plastic products. This method allows you to continuously produce long tubular components with a high degree of accuracy, which can reduce production costs and machine downtime. It also minimizes waste and allows for excess plastic to be gathered and used in future projects. This process is especially useful when producing a product with a large cross-section, such as industrial piping or synthetic filaments.
The extrusion moulding process starts with plastic granules that are stored in a hopper before they’re heated inside a barrel known as an extruder. The granules are then forced through a shaped die, which gives them the desired shape. The resulting linear workpiece is then cooled before it can be cut into plastic parts. The process can be used to create a wide variety of linear products, including food packaging, synthetic filaments, and even drinking straws (coextrusion).
Advantages of Extrusion Moulding
The primary benefits of plastic extrusion moulding include its cost-efficiency, flexibility, and versatility. It’s a good choice for long, elongated products that need to be made with a consistent cross-section, such as pipes, rods, and wires. In addition, extrusion can be used with a wide range of materials, from thermoplastics to metals. It can also be used for products that require a smooth surface and specific textures.
In contrast, injection molding has several disadvantages, ranging from high initial tooling costs to environmental concerns. Its high energy consumption during heating and cooling, along with its limited durability, raise questions about its sustainability. It also does not scale as well as extrusion, which limits its production potential.
Both processes have their benefits and drawbacks, but extrusion is better for making longer plastic items, such as tubes or rods. Injection molding, on the other hand, is better suited for shorter components that need to be precise in size and alignment. However, extrusion has its own unique advantages, such as its ability to produce long lengths of a single plastic material. It’s also great for producing a wide range of colors and textures, which makes it an ideal choice for plastic projects that need to look appealing.
Continuous moulding
Continuous moulding is a versatile process that offers advantages such as shorter cycle times and lower production costs. It is suitable for producing a variety of products, from small, symmetrical items to complex and long-range products. This method is particularly useful for making replacement parts for broken metal items, as it produces very strong and durable results. It also allows for the use of recycled materials.
In this method, a powdered resin is loaded into a hollow mold that is securely closed and heated to melt the polymer. The molten plastic is then fed into a die that gives the final shape to the product. The polymer is then cooled and trimmed to complete the cycle. The advantages of continuous molding are numerous, including the ability to produce complex shapes with high accuracy and precision. It is also an economical and fast way to make replacement parts for damaged metal products.
The main advantage of continuous moulding is its ability to reduce waste, which can be a significant cost in other manufacturing processes. It also produces a uniformly-sized finished product, which is critical for mass production. Additionally, continuous moulding produces a finished part with an extremely smooth surface. This makes it easy to apply coatings, printing, and graphics to the surface of the finished product.
To ensure the quality of a continuous-cast product, the temperature of the molten metal and the speed of cooling need to be closely monitored. In addition, the molten metal must be evenly distributed between the walls of the mold. This can be achieved by using a combination of a cooling system and roller support. A primary additive to the molten metal can improve its flow characteristics during the casting process, while a heat stabilizer prevents thermal degradation.
The most common material used for continuous cast is a blend of low-density and high-density polyethylene. This polymer has excellent chemical and fatigue resistance. It is also readily available in a powdered form and has good flow properties, which makes it suitable for rotational molding. In addition, a range of secondary additives can enhance the mechanical properties of the finished product.
Pressure moulding
Pressure moulding is a process used to produce products that require high levels of detail and precise shapes. This manufacturing method offers many benefits, including low tooling costs and rapid production cycles. However, it is not without its limitations. In order to make the most of this process, it is important to understand its strengths and weaknesses. This will help you determine whether it is the right choice for your project.
The pressure forming process uses heated plastic sheets to shape them over a mold. This is an ideal process for producing thin-walled designs, such as medical devices and automotive components. It is also able to handle a wider range of shapes than vacuum forming. This flexibility is particularly beneficial for companies that need to bring products to market quickly.
However, the high-pressure used in this process can cause thickness variations in the finished product. Inconsistent thickness can lead to weaker areas in the final product, compromising its structural integrity and performance. These variations are caused by the way that the heated plastic material flows during forming. A combination of factors can reduce these variations, including strategic vent placement and optimized mold contours. In addition, using thermoplastics with good elongation and flow characteristics can improve consistency.
Another benefit of pressure forming is that it produces a more uniform part than vacuum forming, due to the fact that the material is heated under constant pressure. Injection molding is a more effective option for manufacturing parts that need to be extremely smooth, though, as it is better equipped to handle complex geometries and thicker materials.
Injection molding is also a better choice for producing larger parts, as it has a greater injection volume than other processes. However, it is important to keep in mind that the pressure of the injection molding machine should be matched to the projected area of the plastic part. Otherwise, uneven heating can occur and the resulting part may be warped or damaged. Likewise, the injection temperature should be adjusted accordingly. Lastly, the injection mold should be designed to allow for quick cooling after injection.